Understand the causes of leakage between ladle slide gate plates,come to know the types of ladle slide gates and related problems of ladle slide gates. If you are interested in ladle slide gate and slide gate mechanism , welcome to visit our factory view manufacture ladle slide gate plates .
1.Installation problem of slide gate plate
(1) Ladle slide gate plate installation surface is not clean, or use too much fire clay when installs upper nozzle, resulting in crack between slide gate plate during casting steel;
(2) Slide gate plate pressure is not enough.
2.Quality problem of slide gate plate
(1) Slide gate plate material can not meet the requirements of casting steel. The harmful ingredients in the slide gate plate exceeded, resulting in increased thermal chemical erosion of the slide gate plate;
(2) There is crack on the slide gate plate when using, and abnormal expansion, the molten steel produces a “V” type melt loss along the crack, resulting in the use of the slide in the slide.
3.Operation problem of casting steel
When the nozzle can not automatically pouring and need to burn oxygen, if the slide gate plate is not fully open in place when burning oxygen, will cause the upper slide gate plate is seriously burned.
The main tasks of the slide gate system
Adjust the steel flow from the ladle to the tundish
Minimize the risk of steel re-oxidation
Efficient management of ladles during steel production
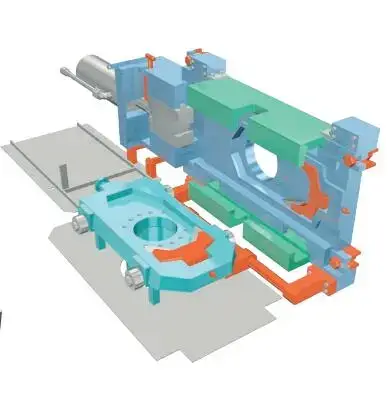
Different Types of Ladle Slide Gate Plates
1.High aluminum slide gate plate
Disadvantages:
(1) Poor corrosion resistance, serious erosion of sliding surface and sprue.
(2) Poor thermal shock stability and easy to crack during use.
2.Aluminum carbon slide gate plate
The aluminum-carbon slide gate plate has experienced non-burned aluminum-carbon and fired aluminum-carbon. In order to improve the corrosion resistance and thermal shock stability of the non-burned carbon slide plate, synthetic mullite, andalusite and silicon carbide materials are added to the pellets, and corundum and silicon carbide are added to the carbonization.
However, in the course of use, the sliding plate of this material gradually has problems such as low thermal strength, serious sliding surface wear and poor crack resistance. The shortcomings of fired aluminum carbon bricks are low thermal shock resistance and cannot be used continuously for many times.
In addition, the carbon is easily oxidized during use, and the corrosion resistance is low.
3.Aluminum-zirconium carbon slide gate plate
The aluminum-zirconium-carbon slide is developed on the basis of firing aluminum-carbon slide. The slide plate of this material uses low expansion rate of Al2O3-SiO2-ZrO2 raw materials, made into a refractory material characterized by carbon bonding with oblique zircon, mullite, corundum, etc. as the main crystal phase, aluminum-carbon slide It has quite good performance and applicability, but the cracking and sliding surface wear in repeated use are the key to restricting the improvement of its life.
Carbon-bonded aluminum-carbon and aluminum-zirconium-carbon slides are currently commonly used slide materials in steel mills at home and abroad, but these two slides have poor calcium corrosion resistance when casting calcium-treated steel, and are not suitable for calcium-treated steel, Al/ Casting of Si-killed steel and other steel grades.
4.Magnesia carbon and spinel carbon slide gate plate
Magnesium slide gate plates were first used in Europe. Because magnesium oxide has good resistance to mechanical stress and chemical corrosion, it meets the requirements of cast calcium-treated steel and high-oxygen steel to a certain extent.
However, the coefficient of thermal expansion of the magnesium oxide slide plate is large, and it is prone to thermal spalling when casting steel, and the thermal shock resistance needs to be improved.
Spinel carbon slide is a refractory material that uses magnesium-aluminum spinel as the main crystal phase and is characterized by the combination of ceramic and carbon.
The thermal expansion coefficient and elastic modulus of magnesium aluminum spinel material are both smaller than that of magnesium oxide, and its thermal shock resistance is stronger than that of magnesium oxide. However, the spinel material and the calcium in the steel have a slow chemical reaction, resulting in low-melting substances that affect its service life.
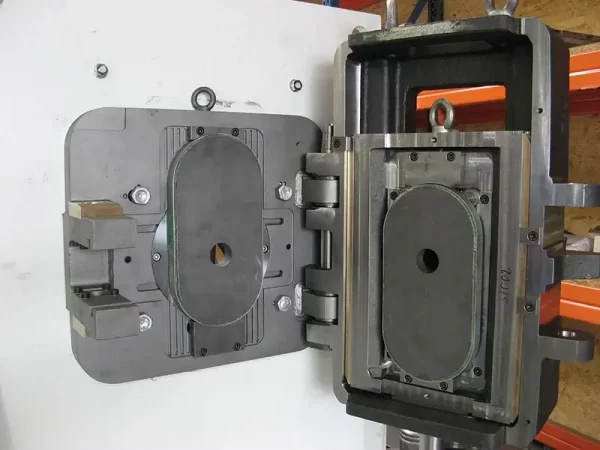
What is slide gate in ladle?
The function of a ladle slide gate system is to precisely control the steel flow from the ladle to the tundish.
What is the use of slide gate plate?
Slide Gate Plate Refractories are installed on the ladle’s bottom for regulating the flow of liquid steel from Ladle to Tundish. These are special refractories and should be treated with caution. Failure could lead to a severe catastrophe.
What is slide gate refractory?
Slide gate refractories are used for a wide range of applications. Specific physical, chemical and mineralogical compositions of high purity ensure high corrosion and erosion resistance, optimum thermal shock resistance to yield optimum performance.
What are ladle slide gate plates made of?
The slide plate of this material uses low expansion rate of Al2O3-SiO2-ZrO2 raw materials, made into a refractory material characterized by carbon bonding with oblique zircon, mullite, corundum, etc.