1.Causes of cracks in high alumina brick molding and improvement measures
High-alumina bricks are usually formed by friction presses or automatic brick presses of more than 300T. The biggest feature of cracks caused by reasons such as product brick shape, forming mold, uneven distribution, operation and pressure is strong regularity, and the depth, position and direction of the cracks are basically consistent.
1) Reasons for brick shape: Since different brick shapes are pressed with different molds, the structure design of the mold with holes, tongues, grooves or corners is unreasonable. There are many tongues and grooves and they are not easy to form on the mold side surface. The mold sides on both sides are movable plates, which are very easy to cause cracks after demolding.
2) Unreasonable design of molding mold: Since the molding mold design lacks exhaust grooves and exhaust holes, cracks are prone to occur when the brick blank is molded and molded.
3) Unreasonable installation and use of molding mold: Unreasonable mold installation, cracks are prone to occur when the brick blank is molded and molded. During the use of the mold, after the mold is worn, the model and the mud are rubbed against each other during the molding process, and the surface finish and hardness of the mold wall are worn to a certain extent, which is easy to cause cracks in the holes, tongues, grooves or corners.
4) Reasons for uneven distribution: Uneven distribution can easily lead to different densities between the edge and the middle of the high-alumina brick blank. During the drying process, the density of the surrounding area is lower than that of the middle, and the temperature of the edge is higher than that of the middle, which leads to faster evaporation of moisture at the edge and slower evaporation of moisture in the middle, resulting in a situation where the dehydration rate of the edge is greater than that of the middle. When the edge dehydrates and shrinks too quickly, cracks will appear on the edge of the blank.
5) Reasons for molding operation and molding pressure: During the molding operation, “short-range fast beating” and “full-range hard beating” are used. Although most of the gas is exhausted, a small part of the gas is still compressed and not completely exhausted. When this pressure exceeds the fracture strength of the brick blank, it will cause internal transverse cracks in the brick blank.
Improvement measures
1) For bricks with holes, tongues, grooves or corners, appropriate chamfer and taper parameters can be designed, and a small amount of graphite and oil mixture can be brushed on the mold before pressing to facilitate the demolding of the bricks and reduce cracks caused by unreasonable mold structure design.
2) Reasonably design the mold, and process 2mm (width) × 1mm (depth) exhaust grooves on all top and bottom plate sides, with a spacing of 100mm, to facilitate the discharge of gas during the molding operation and reduce cracks when the bricks are molded and demolded. In addition to processing the exhaust grooves on the mold, all products have additional exhaust holes on the top plate surface, with a diameter of 6mm~qb15mm, distributed at intervals of 100~150mm along the length direction. Length < ̄230mm, 1; 230~400III1TI, 2; >400mm, 3. And process 5mm (width) × 2mm (depth) horizontal channels on the non-working surface to facilitate exhaust. By taking the above improvement measures, the internal cracks generated during the molding and pressing of the bricks are greatly reduced.
3) Install the forming mold reasonably, and a full-time model quality inspector is responsible for on-site inspection and acceptance of the model, check the brick type and size of the model, and record the acceptance situation one by one. At the same time, strengthen the inspection of the use of the mold, and weld the mold with a large degree of wear in time to reduce the cracks of the semi-finished product caused by mold wear. For varieties with complex brick shapes, the production difficulty can be reduced through measures such as model improvement, and the production efficiency and product quality can be improved.
4) During the forming operation, pay attention to uniform distribution, so that the density of the edge and middle parts of the high-alumina brick blank is basically the same, and reduce the cracks caused by the different density of the blank body and the middle part during the drying process.
5) During the forming operation, press the brick according to the operating procedures, light first and then heavy, slowly pressurize, ensure the number of pressings, and be careful not to “short-range fast hitting” and “full-range hard hitting” to reduce the generation of internal cracks.
2.Cracks in high alumina bricks caused by mud
The critical particle size, the amount of fine powder added, and the quality of the mixed mud will affect the cracks in the semi-finished high-alumina bricks. For example, the matrix material is generally composed of fine powder, which shrinks during the firing process, while the particles generally expand. The large deformation difference between the two causes internal stress, which causes cracks in the product.
Improvement measures
When mixing the high-alumina brick mud, the order of adding materials must be strictly controlled. When mixing, first add the granular material and dry mix for 1 to 3 minutes, then add the pulp binder and mix for 23 minutes, and finally add the fine powder and mix for 6 to 8 minutes. The effective mixing time of the pulp is not less than 10 minutes. The conventional control parameters of the mud particle size of aluminum bricks are: 32mm, 18%±5%; 0.5~O.1mm, 15%±5%; <0.1mm, 40%±5%. The moisture content is <1.5%. In actual production, the critical particle size and the amount of fine powder added can be adjusted. At the same time, an appropriate amount of expansion agent or granular materials with a smaller thermal expansion rate can be introduced, and reasonable mud control parameters can be formulated to improve the mixing quality of the mud.
3.Reasons for cracks in high alumina bricks due to raw materials
Cracks in high-alumina bricks are a common cause of waste in the production process of high-alumina bricks. Impurities (especially K2O and Na2O) and the degree of sintering in high-alumina bauxite clinker, the main raw material for producing high-alumina bricks, will cause cracks on the surface of the product. The poorly sintered clinker continues to shrink unevenly during the firing process of the product, causing the product to crack and crack; at the same time, during the firing process of the product, the secondary mullite transformation (3α—Al2O3+2SiO2→3Al2O3·2SiO2, 1200~1500℃) of the poorly sintered clinker itself continues. Secondary mullite transformation mainly refers to the reaction of SiO2 combined with clay and Al2O3 of high-alumina clinker in the production of high-alumina bricks to form mullite, accompanied by volume expansion (about 10%), resulting in inconsistent shrinkage of the product, leading to an increase in the number of cracks on the surface of the product and an increase in the degree of cracking.
Improvement measures
The main mineral components of high alumina bricks are mullite, corundum and glass phase. With the increase of Al2O3 content in the product, the amount of mullite and corundum phase also increases, the glass phase decreases accordingly, and the refractoriness and high temperature performance of the product are improved accordingly. In the actual production of high alumina bricks, attention should be paid to controlling the impurity content of the high alumina clinker used. According to the requirements of YB/T, 5179-2005 (High Alumina Clinker), the content of K2O and Na2O is ≤0.35%~0.6%, and raw materials with low impurity content and good sintering degree should be used for production as much as possible. Generally, the sintering degree of clinker is judged by testing the water absorption rate of clinker. In the production process, clinker with low water absorption rate can be used to produce high alumina bricks, which can effectively reduce the cracks on the surface of the product. Practice shows that in order to avoid and reduce the generation of network cracks on the surface of high alumina bricks, the water absorption rate of GL-50~GL-90 high alumina clinker is controlled below 2.5%~5.0%.
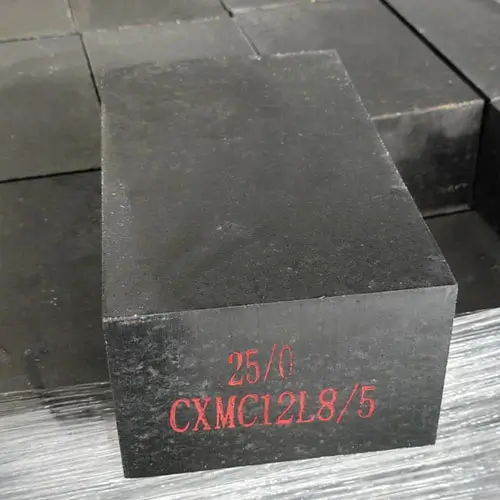