Electric arc furnace is a kind of electric furnace that utilizes electric arc energy to smelt metal. Industrial application of electric arc furnace can be divided into three categories: the first category is direct heating type, the arc occurs in the special electrode rod and be melted between the charge, the charge is directly subjected to the arc heat. Mainly used for steelmaking, and secondly also used for melting iron, copper, refractory materials, steel refining, etc..
The second type is indirect heating type, the arc occurs between two special electrode rods, the charge is subjected to the radiant heat of the arc, used for melting copper, copper alloys and so on. This kind of furnace noise, poor melting quality, has been gradually replaced by other types of furnaces.
The third category is called mineral heat furnace, is a high resistivity ore as raw materials, in the working process of the electrode is generally buried in the lower part of the charge inside. The heating principle is: both the use of electric current through the charge, the resistance of the charge to produce heat, but also the use of the electrode and the charge between the arc heat. So it is also called arc resistance furnace.
The electric arc furnace wall is divided into three parts according to the conditions of use: the main wall, the slag line and the hot spot.
①In the main furnace wall part of high power and ultra-high power electric furnace, mainly use direct bonded magnesium-chromium bricks, pre-reaction magnesium-chromium bricks, magnesium bricks and so on.
② hot spot parts close to the arc, subject to high temperature radiation and slag spatter, damage is particularly serious, the main use of oil-impregnated magnesium bricks, direct combination of magnesium-chromium bricks, cast magnesium-chromium bricks, magnesium-carbon bricks and so on.
③ slag line part of the steel and slag by the serious erosion, the use of poor conditions, should be used with hot spots similar to high-quality refractory materials.
Due to the different working conditions of the various parts of the furnace wall, the use of a single material masonry is not much, most of the use of a variety of bricks integrated masonry, in order to equalize the erosion. In the upper part of the furnace wall, slag line and hot spots, due to the thermal load, chemical erosion and mechanical effects caused by uneven erosion is the weak area of the furnace wall, “hot spots” and even restrict the service life of the furnace wall. In order to adapt to the needs of these harsh erosion parts, erosion resistance, heat shock resistance, small linear expansion rate of magnesium-carbon bricks, in the high erosion area of the increasing use of electric furnaces, it has become the first choice of refractory materials for the wall of the domestic and foreign UHP electric furnaces.
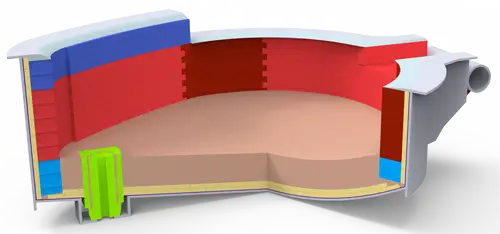
What are the differences between the refractory materials used for lining the walls of domestic and foreign electric furnaces?
The United States in the 1960s, the electric furnace wall began to use high temperature firing directly bonded magnesium-chromium bricks. 70’s to meet the needs of large electric furnaces and UHP electric furnace hot spot area, the trial of fused magnesium-chromium bricks and then combined with magnesium-chromium bricks integrated masonry. 1976 in the UHP electric furnaces on the extensive use of “Corhart” fused magnesium-chromium bricks, 90% ~ 95% masonry for slag line area, partly for the slag line area. 90% ~ 95% in the hot spot, part of the slag line area. Fusion casting brick magnesium-chromium spinel direct combination of high degree, dense structure.
In the mid-1970s, the U.S. electric furnace steel development is very fast. A major development to effectively improve the productivity of electric furnace steel is the development of the use of raw materials and process costs in the high loss area of the electric furnace wall, but the use of magnesium carbon bricks with good results. Raw materials used CaO/SiO2 = 3 high-purity, high-density sintered magnesium sand production of magnesium-carbon bricks, containing about 10% carbon, the apparent porosity of 3%, bulk density greater than 2.95g/cm3.
Most of the former Soviet Union electric furnace wall with magnesium materials, had to fused magnesite and chrome ore trial production and then combined with magnesium-chromium bricks, used in 100t electric furnace erosion serious parts of the upper part of the outlet, the brick low melting point of the mineral phase is less, erosion resistance, the use of the effect is better.
British electric furnace wall, generally with ordinary chrome magnesium bricks (70% chrome ore, 30% seawater magnesium sand) and sintered magnesium chrome bricks (70% seawater magnesium sand, 30% chrome ore) as well as seawater magnesium sand production of ordinary magnesium bricks phase high-quality magnesium bricks and so on. In the hot spot and slag line parts with seawater magnesium sand preparation of high temperature fired magnesium bricks or by the asphalt, tar soaked sintered magnesium bricks, to obtain a good use of the effect.
Japanese electric furnace wall using magnesium chromium brick, magnesium brick, hot spot parts using magnesium brick, magnesium carbon brick, fused magnesium chromium brick, carbon brick and so on.
In the 1980s, China’s electric furnace steelmaking has made rapid development, has been developed from ordinary power electric furnace to ultra-high-power electric furnace, electric furnace steelmaking technology advances are closely related to the synchronous development of refractory technology, promoting the electric furnace furnace age steadily improve, refractory unit consumption gradually reduced. China’s ordinary power electric furnace used two kinds of furnace lining, one is in the sintered magnesium sand and electrofused magnesium sand with low and medium temperature binding agent of the pounding material overall furnace lining; another is tar bonded magnesium brick and different standard magnesium carbon brick masonry furnace lining. Alkaline carbon-containing products are the main materials for furnace wall lining, and magnesium-carbon bricks used in electric furnaces play an important role.
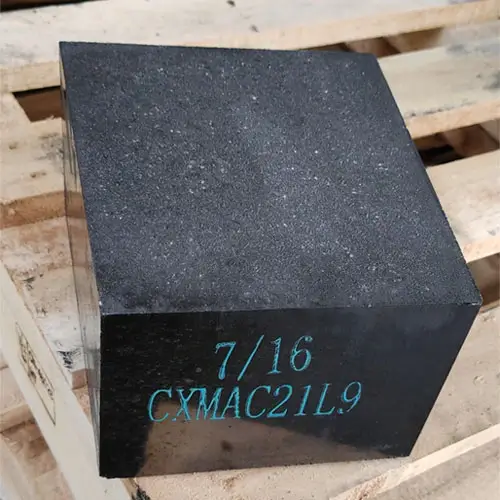